Table Of Content

Hermogeno and designer Lynette Chin brought in a mix of vintage and new furnishings in the family room, incorporating performance fabrics for durability. “[We made] sure that it was a really usable room, that it didn’t just look nice,” Hermogeno says. Hand-painted floors were the jumping-off point for designer Amy Peltier’s soothing primary bedroom design. “It was so much work, but it turned out beautiful.” The firm wanted the space to feel “light and airy and breezy,” and incorporated fabrics and wall coverings by Thibaut in a soft color palette. Peltier and designer Marina Kelly installed an arch to divide the bedroom from the sitting area, breaking up the large space.
Tiger Woods is changing an important piece of gear Wall-to-Wall
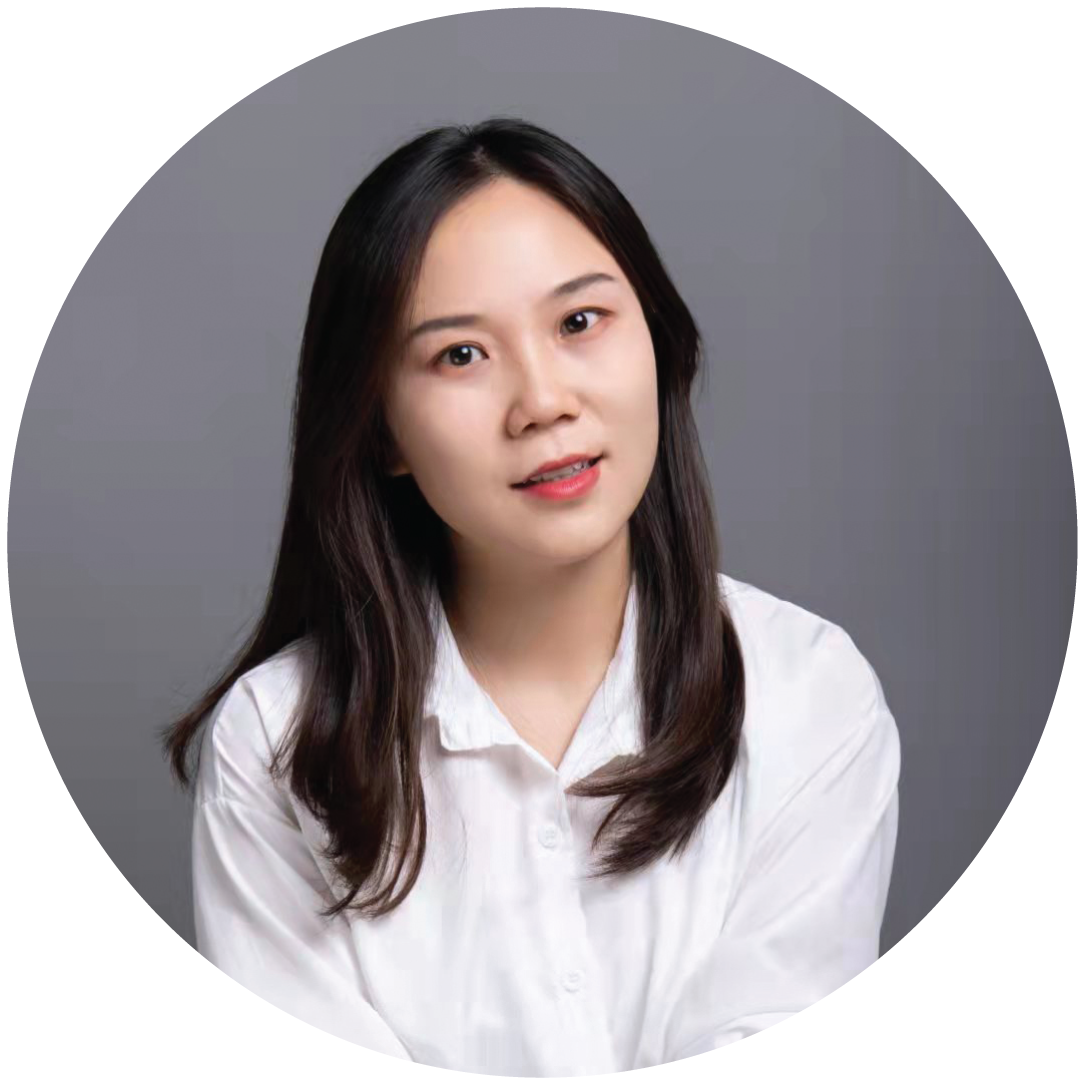
It focuses on achieving optimal output quality by reducing product defects. DFSS uses a range of statistical tools to determine what the needs of customers are and what the goals of the business are. Using DFSS, customer needs must be considered when making any decision at any stage of the product development process. The Design for Excellence methodology involves systematically scrutinizing every aspect of the product development process from the design stages to the manufacturing phase. With every task they undertake, stakeholders must strive towards achieving a clear objective. In this way DFX helps to eliminate errors, reduce waste, and ensures efficiency and quality throughout the entire development process.
Rigor, Reliability, and Results through a focus on design outcomes
It allows project teams to reduce costs, accelerate timelines, improve quality, and increase customer satisfaction. Our digital quoting platform can make recommendations on improving cost and production. With injection molding, for example, we can make recommendations on tool (mold) life. This tool compares prototyping vs. on-demand manufacturing options so you have full visibility regarding total cost of ownership for your molded parts. But, whether it’s us or another digital manufacturer, you will be able to adjust items such as materials, quantity, turn time, and other cost variables to see the pricing implications.
New Apple Watch redesign rumors
DfX removes these challenges to the early stages of the design process, saving cost and time. Though DfX and traditional engineering methods have many similarities, they have notable differences. Here’s a short list of examples to improve product development by designing parts through different X variables. There are also standalone software packages like ParaMatters and nTopology that are focused exclusively on automated design optimization that can be used alongside traditional 3D design software. At the time of the first order, you may not have a precise idea of what your target market wants — that’s quite dangerous, as some companies launch manufacturing of too many colors, sizes, and/or other variations.
Computer-Aided Engineering
Our Design Studio makes it easy to create a custom shirt from scratch. Use our text editor to add text or pull from our clip art library to personalize the look. If you already have a design then you can upload it and set the placement. We guarantee that you’ll get a great apparel design no matter what your budget is. Our higher-priced packages offer more experienced designers and more hands-on support.
Saving Lives with Accelerated Development of Mechanical Ventilators
Having to do complex disassembly and reassembly, or having to replace half the entire product when only one part has an issue, is to be avoided if possible. Some companies took that to an extreme and went for modular construction, which means each part can be replaced separately over time. Even when a major breakdown occurs, following design for maintenance gives easy access to the parts that could be the most probable culprits. For example, you can easily change spark plugs and the like in cars while accessing motor belts requires considerably more work. Having it vice versa would not make sense as changing plugs is a job that needs to be done with much higher frequency.
DfX vs Traditional Engineering
Closing the loop on these materials is a crucial step towards a more sustainable future. With the ability to differentiate PA 6 and PA 6.6, trinamiX helps brands close this loop. For example, BASF has utilized trinamiX technology to qualify PA 6 waste streams for their new loopamid® product, the first polyamide 6 entirely made from textile waste.

As stated before, the scope of DFX is broader and more inclusive than regular engineering design. By utilising the design principles within the various areas (for example, DFM and DFA), the DFX methodology increases the value while reducing the costs of products. Design for excellence is an ever-evolving philosophy of a set of principles in design and manufacturing. It adopts a holistic and systematic approach to design, focusing on all aspects of a product – from concept generation to final delivery. Packaging Design has a significant impact on a product’s sortability, and therefore recyclability. If a container cannot be identified properly by NIR, it has high probability of ending up in a landfill.
This ensures ease of testing later on, reducing test costs and time. Design for X (DfX) or Design for Excellence refers to a set of methodologies focused on optimizing the process of product design for a specific objective, which is represented by “X”. The “X” can stand for qualities like manufacturability, reliability, quality, or cost-effectiveness. Before creating the product, it is critical to design for testability, supply chain, manufacturability, quality, and other factors. Exceptional engineering design methods begin with a thorough evaluation, are delivered early, and avoid future redesign.
The focus in DFS is on reducing the carbon footprint of the product by using recyclable materials and green manufacturing ideas for the product as well as its packaging. Design and manufacturing teams get together to design a better product than what each of them would have come up with were they to work alone. It is one of the most common and useful design for X categories as it provides techniques that help us create a better product at a lesser cost. Designers use them to enhance the design of parts, assemblies, and complete products.
Traditional engineering design involves many versions of a product. Design for Excellence, another name for this term, refers to a set of methodologies, principles, and criteria for developing high-quality products during the concept design stage. Design for manufacturing (DFM) – the most common and most foundational of the “Design for X” approaches. Design for manufacturing makes sure that the parts that will make up your full product can actually be made with materials and processes that are relatively common and mature, in a way that supports your overall design intent.
Of course, those are important, but there are other important questions such as “can it be made with mature processes? ” (a.k.a. Design for Manufacturing), “can it be assembled easily and without mistakes? In many cases, testing consumes a good portion of the project budget, especially if testing methods are put in place after the design and manufacturing aspects have been finalised. This must be done from the earliest stages of the design phase and evaluated at every stage after that. Integration into the entire product development process is a requirement to achieve the best results.
No comments:
Post a Comment